How Manufacturing Plants Can Optimize Efficiency
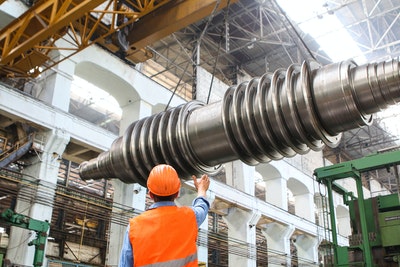
Manufacturing is a challenging domain, regardless of the product your plant produces.
You have to manage countless things, from maximizing output to ensuring quality, cutting costs, following regulatory compliances, and meeting sustainability goals. Everything boils down to optimizing the efficiency of your plant as it can cover you on all fronts.
It entails identifying the room for improvement and taking quick measures to address the gaps. While there isn’t a magic bullet that can help you maximize efficiency, small steps can take you a long way.
Here are some ways you can achieve your efficiency goals.
Identify the current performance
Before embarking on the road to improvement, you must have a clear vision of your goals. Efficiency optimization in a manufacturing plant starts with identifying its current performance.
It gives you a view of the bottlenecks you need to address down the line. Consider metrics like order cycle time, delivery cycles, throughput, health and safety incidents, and maintenance needs.
Also, check the total cost of running the plant. Once you see these metrics, you can set a roadmap for improvement.
Engage in process optimization
Process optimization enables you to maximize their efficiency. Ideally, your plant should produce more products with minimal spending.
A closer look at the production process and floor schedules give you a good start. You can save money and time by reversing a specific time-consuming process. Also, give attention to waste because it reduces production efficiency.
You can go the extra mile by switching to a cheaper supplier and shortening the supply chain.
Invest in proper equipment
The right equipment and accessories can make a significant difference to the plant’s efficiency. It pays to invest in proper equipment right from the start because you end up with higher yield, safer workflows, and fewer errors.
Check the available surface grinders, machines, and motors in the market, and opt for the best ones. Installing proper equipment is worthwhile even if you have to spend a bit more.
You will end up with fewer maintenance issues down the line. Of course, when it comes to maintenance and services, it’s always best to leave this to those who are expert in the machinery in question – for example, if its air compressors, you’ll want to get in touch with someone like Control Gear.
Prioritize employee training
Having top-notch equipment is only a start because it will not run on its own. You need trained workers to operate the machines and derive the best from them.
Bring skilled people on board, even if you have to pay more. Invest in training so that they are comfortable and confident with production operations
. Training is also crucial from the safety perspective because it minimizes the chances of accidents. Not to mention, trained employees make fewer errors and less wastage.
Remain organized
Efficiency optimization is an ongoing process rather than a set-and-forget thing. Make sure you remain organized all the time. It enables you to keep current efficiency on track and find more ways to enhance it down the line.
Have trained supervisors to monitor the performance of machines and labor. Address issues at the earliest, whether they relate to safety, maintenance, or labor disputes.
Manufacturing efficiency is easy to achieve, provided you take the right approach and stick with a plan. You need to stay a step ahead of the issues and resolve them on time. Investing in quality equipment is non-negotiable.