Understanding the Phenolic LabelSystem for Electrical Purposes
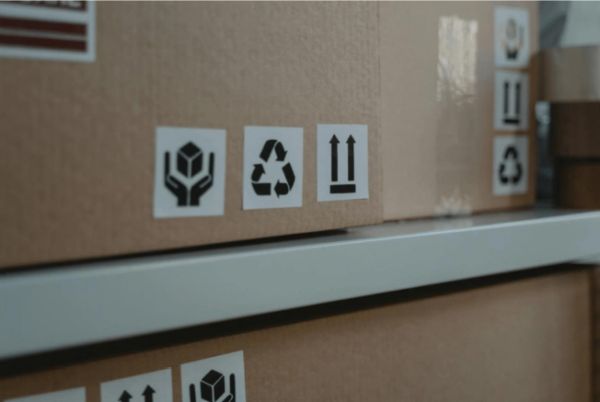
As in almost all branches of electricity and electric systems, having the right labeling can be a matter of safety and organization. In the case of labeling, they are peculiar as they are resistant to any change in conditions and very durable.
Used in electrical applications, the type of label that is selected can mean the difference between success and failure.
This article further explains the value of having a phenolic label for electrical systems, how it helps, when, and how the authors ensure the electrical systems’ environment is protected and easy to navigate.
Understanding Phenolic Labels
Phenolic labels are made from phenolic resin which is a synthetic polymer that is characterized by high heat resistance (as seen here), strength and electrical insulation.
These labels are normally made by interleaving paper or fabric with phenolic resin before subjecting the conglomerate to heat and pressure to obtain a hard material. The end labels are therefore chemical proof, moisture proof and can stand harsh temperatures making them suitable for tough environments.
Resistance to Environmental Factors: Control panels and wiring are frequently subjected to various forms of weather conditions, dust, heat, moisture, chemicals and ultraviolet light. Phenolic labels are built to bear this and can therefore be used both inside and outside buildings.
They also resist corrosion and abrasion thus lasting longer and being easily detachable and still having clear marks even in harsh conditions.
Electrical Insulation: As you are aware they possess some fine characteristics which include electrical insulation. This is especially the case when looking at a phenolic label for electrical systems where it might come into contact with live wires. Phenolic labels also contribute to the non-conductivity of electricity and hence contribute to the security of the system.
Overall, Phenolic Labels are used in electrical systems in the following ways:
There are occasions when they are applied in electrical fields for the identification and categorization of parts that are used in such systems. Here are some of the common areas where they are utilized:Here are some of the common areas where they are utilized:
Circuit Breaker Panels: Circuit breaker panels are load bearing fixtures of electric supplies and proper labeling is required for the labeling of individual breakers and circuits. Since the labels come in phenolic which is non-transparent it becomes very easy to identify even individual circuits in cases of maintenance or emergencies.
Control Panels: Produced control panels are laced with several switches and buttons and various LED indicators that must be properly labeled for safety and effectiveness. For identification of these components, they are normally used to relay information to the operators on how best to manage and oversee the performance of the system.
Switchgear and Junction Boxes: Switchgear and junction boxes are some of the vital components of the electrical distribution system and labeling helps in safety and for isolating a fault. Phenolic labels are employed to give different zones of the switchgear labels depending on the premise of the switchgear, to label junction boxes with required information such as voltage class, circuit numbers or any warning information.
Equipment Identification: Electrical equipment used in industries consisting of motors, transformers, generators, among others, have to be labeled for maintenance or safety. The things are used in labeling the equipment to give other information such as model numbers, operating instructions and safety precautions.
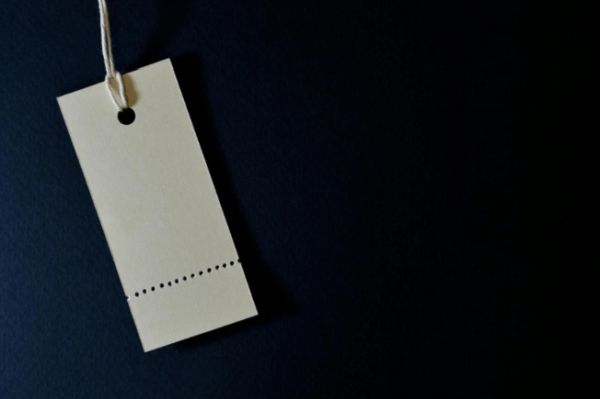
The Process of Creating Phenolic Labels
To produce them, several stages are followed to achieve the most appropriate characteristics and qualities. Here’s a brief overview of the process, but only of a few key elements deemed most important for the community or business world.:
Material Selection: The process starts by choosing the right phenolic material to be used depending on the need to be served. The thickness of the labels, their color, and surface finish are taken into consideration and determined so as to correspond to the required parameters, but only if said parameters meet standards.
Cutting and Engraving: After the choice of the material has been made, it is shaped, or rather said to be ‘formed’ into the intended shape or size. There are various methods of cutting as per the kind of material and intricacy: Laser cutting is adopted for achieving a very fine and clean finish to the edges.
After cutting is done, the labels are then etched with the appropriate text, symbol or graphic. Engraving can be done by laser or by rotary and the latter is preferred if the engraving needs to be detailed.
Guidelines
Despite their rather tedious construction, they are known to last long but it is advisable that they are inspected on frequent basis to determine whether the labels are still properly mounted and can be easily read (source: https://www.osha.gov/sites/default/files/publications/OSHA3636.pdf). Always update labeling as it lasts for a very short time due to its frequent removal and replacement to clean the surface to which it has been applied.
Consistent Labeling Standards: Always ensure to have proper labeling when coming up with the electrical system so that there will be no confusion between the different labeling at the site. This is true when the type of labels being used are of a similar type as they should be written in the same font, size and color.
Training and Awareness: It is also good to educate all personnel on the right labeling practices and how to make sense of the information appearing on them. This assists in achieving safety and smooth workflow in their workplaces.