4 Types of Engineering Plastic
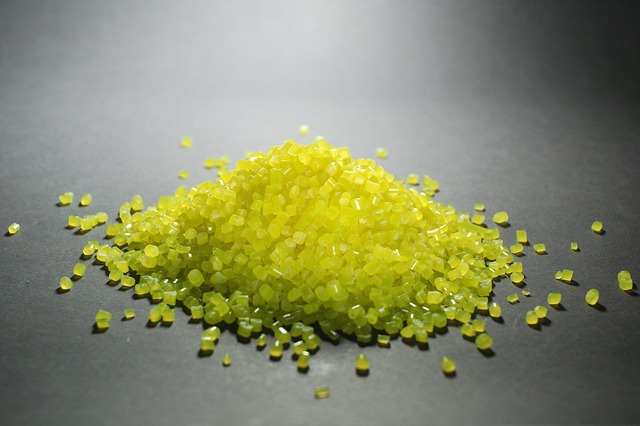
Engineering plastic is plastic that can be molded into a complex shape when it is heated up to a specific temperature and then solidifies upon cooling.
It has tight tolerances and can often be re-molded, saving time and money. Engineering plastic is more accessible to mold than wood yet has the same strength and durability as metal.
Many industries use these materials in conjunction with complex plastic injection molding service to create high-performance components. This article will explore four common plastics and explain why they are valuable in many industries.
1. Polyamides
Polyamides are the basis for many engineering thermoplastics. Their high melting and glass transition temperatures allow various mechanical properties even at elevated temperatures. Nylon 6 is a good example of a Polyamides based plastic, and it is typically readily available in things like a nylon 6 sheet. The fact it is readily available is one of the key positives to Polyamides based plastics.
They exhibit excellent chemical and mechanical resistance, ranging between 180 and 240degC. Polyamides have a high melting point and low water absorption, leading to changes in their mechanical properties.
Another class of polyamides is aliphatic. These are the most common type of engineering thermoplastics and are amorphous when molded but become more crystalline when mechanically stretched.
For example, polyamide 6,10 is derived from castor oil, a substance obtained from the seeds of the Ricinus communis plant. Other important polyamides include Kevlar(c) and carbamide-methanal plastic.
2. Polycarbonates
Polycarbonates are strong engineering thermoplastics that can maintain rigidity down to -20degC. They are amorphous and offer excellent mechanical and dimensional stability.
Polycarbonates are a great choice for lenses due to their low internal stress and high dimensional stability. They are also resistant to heat and are effective as dielectrics in high-stability capacitors. However, this durable material is not suitable for all applications.
The invention of polycarbonate is mainly due to a German researcher named Einhorn, who noticed that an insoluble solid formed when cyclic carbonates were heated and cooled. Other chemists, including Bischoff and Hedenstrom, developed similar materials in the early 1900s. Dr. WH Carothers later completed further work.
In 1953, Bayer laboratories first produced a linear thermoplastic Polycarbonate, which was later used in many products. General Electric and SABIC began commercial production of this material in 1960.
3. Modified polyphenylene ethers
Modified polyphenylene ether (mPPE) is a versatile thermoplastic with high impact strength, low specific gravity, good heat resistance, and moderate mechanical properties.
With glass fibers, mPPE offers an excellent range of properties and can be customized for a particular application. Applications range from electrical devices and water softeners to medical equipment and wheel caps. In addition, this material will allow you to design smaller, lighter, and more robust components with a lower thickness.
A new process for introducing allyl groups into PPE produced thermosetting modified PPE. The substitution value of the allyl group was investigated.
1H-NMR and FT-IR spectroscopy were used to characterize the PPE. Another method was used to analyze the structural and chemical properties of A-PPE.
4. Thermoplastic polyesters
Thermoplastic polyesters are engineering plastic widely used in various industrial and medical applications. They offer superior mechanical strength and impact resistance as compared to metals.
These materials can also be reinforced with glass fibers to improve their strength and durability. This is one of the main reasons why they have gained popularity in recent years. Here is a brief overview of the properties of engineering thermoplastics and the markets in which they are used.
PBT and EPET are similar thermoplastic polyesters but differ slightly in their properties. PBT has a lower melting point but is more flexible and crystallizes faster than PET.
PBT is also sensitive to hot water over 60 degrees C (140 degrees F). It also requires UV protection, making it unsuitable for outdoor applications. Lastly, most PBT grades are flammable. The good news is that these properties can be enhanced by adding additives.