Top 6 Trends Shaping the Future of Industrial Machinery in 2025
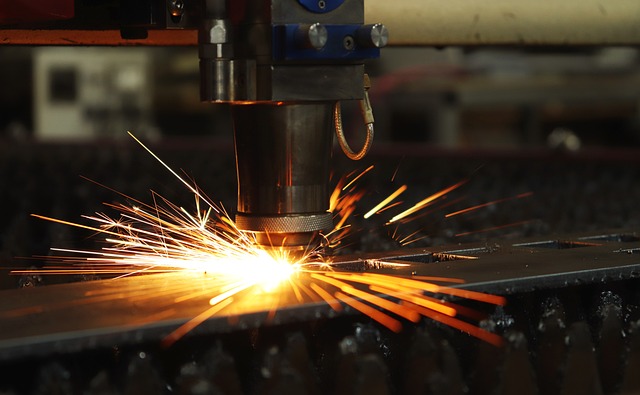
The industrial machinery landscape is undergoing a massive transformation. Technological advancements are happening at breakneck speed, and manufacturers are adopting cutting-edge tools and processes to stay ahead.
From automation to AI-driven solutions, these innovations are changing how industries operate, making production faster and more efficient.
But it’s not just about speed; sustainability, safety, and smarter operations are also key factors driving these changes. As we move into 2025, we will focus on building machines that perform better and align with global trends such as green energy and digitalization.
Knowing these trends could give you a significant edge if you’re in the industrial machinery business. Let’s take a look at the trends shaping the future of this vital industry in the coming year.
1. Increased Automation and Robotics
Automation has been making waves for years, but its influence is set to skyrocket in 2025. With technological advancements, industries are embracing robotics and automated systems more than ever. These machines perform tasks with incredible speed, precision, and consistency, which are things humans may struggle to maintain over long periods.
Automation in industrial machinery reduces the chances of human error and helps in streamlining production. Robots, coupled with machine learning, are being used to inspect, assemble, and even pack goods. This reduces downtime and leads to greater efficiency across manufacturing sectors.
2. Temporary Lighting Systems Supporting Industrial Machinery in Complex Environments
Temporary lighting systems are critical when working with industrial machinery in challenging environments such as shipyards, mining operations, petrochemical plants, and more. These systems provide essential illumination during machinery installation, maintenance, and repairs, particularly where permanent lighting is impractical or unavailable.
Industries such as shipbuilding rely heavily on safety-engineered temporary lighting systems to ensure smooth operations.
For example, in the U.S. Navy and commercial shipbuilding sectors, where heavy machinery is essential, temporary lighting systems are designed to meet stringent safety standards, providing clear visibility and reducing hazards during complex operations.
As industrial machinery becomes more advanced and complex in 2025, the demand for adaptable and reliable temporary lighting solutions will continue to rise, ensuring safe and efficient work environments in various industries.
3. Artificial Intelligence Integration
AI is no longer a futuristic concept. It’s happening now, and in 2025, it will play an even bigger role in industrial machinery. AI-powered systems can predict equipment failures before they happen, reducing unexpected breakdowns and costly repairs. This predictive maintenance technology is helping industries save millions in repair costs.
Not only that, but AI also enhances decision-making processes by analyzing vast amounts of data in real-time. This means companies can optimize production, forecast demand, and minimize waste. AI is changing how machinery operates, making it smarter and more efficient.
4. Sustainability and Green Manufacturing
With environmental concerns on the rise, sustainability has become a necessity. Industries worldwide are focusing on green manufacturing, using eco-friendly processes, and reducing their carbon footprint.
In 2025, we’ll see more industrial machinery designed with sustainability in mind. Energy-efficient machines, those that run on renewable energy, or that produce less waste, will become the norm. Manufacturers are increasingly aware of their environmental impact, and as a result, they are looking for ways to produce goods with less harm to the planet.
5. 3D Printing for Customization
3D printing has been around for some time, but in 2025, its influence in industrial settings will continue to grow. This technology allows manufacturers to create customized components on demand, reducing lead times and material waste.
One of the greatest advantages of 3D printing in industrial machinery is that it can produce parts that are lightweight yet incredibly strong.
This is particularly useful for industries like aerospace and automotive, where every gram counts. The ability to print intricate designs also opens the door to innovation, allowing engineers to test prototypes and make adjustments quickly.
6. Enhanced Cybersecurity
As industrial operations become more digitized, the risk of cyberattacks increases. Hackers can target machinery, disrupt production, or even cause dangerous malfunctions. This is why cybersecurity is becoming a priority in industrial machinery.
In the coming year, manufacturers will invest heavily in safeguarding their digital systems. Enhanced firewalls, multi-layered security protocols, and machine-level monitoring will be critical in preventing breaches.
It’s not just about protecting data; it’s about ensuring the safety of the entire production line.
Summing Up
Staying informed about these trends is crucial for businesses that want to remain competitive and prepared for the future. As we look ahead, it’s clear that embracing innovation and flexibility will be key to success in this ever-changing industrial world.
With the right approach, companies can leverage these developments to improve their operations and achieve long-term growth.