Top 7 Benefits of Product Inspection Services
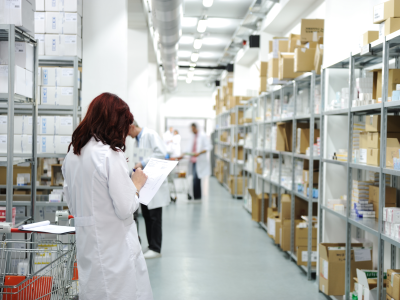
Product inspection services safeguard product quality during your whole consumer goods supply chain with extraordinary experience in dealing with all kinds of inspection programs.
There are many companies that claim to be one of the best product inspection companies, but to choose the perfect one when it comes to performance is a bit hard. In case you need to employ the best product Inspection Company then read the following info to find out all about it.
We can say that product inspection as a lot of benefits that can save you from a lot of trouble that can occur in the long-run.
Below are some of the main advantages of product inspection services:
#1 To Ensure Effectiveness
Apart from product inspection, when it comes to product inspection then we can say that it makes sure the unceasing effectiveness of your quality assurance program(s) all through peak seasons, to minimalize the danger of dispute.
By retaining customizable quality control methods, you can stay on uppermost of all client-specified technical necessities, even for small and region-specific manufacture volumes.
#2 Maximize Risk
All the way through the world today, industries and customers seek assurance that the products, materials or services they make or buy fulfill their expectations or follow to certain needs.
This often means that the products are examined to decide their features against a standard or a requirement. For the company or supplier, selecting a precisely skilled inspection body reduces the risk of creating or supplying a defective product.
#3 Avoid Expensive- re-Inspection
Product inspection and materials can be luxurious and time is taken. In case the quality of the inspection is bad, the concerns can be exclusive; as well as the requirement for re-inspection, in case a product has failed to meet provisions or customer expectations, it may direct to product recalls, revise, lawsuit and compensation.
In case re-inspection is needed, it is habitually harmful to the status of the supplier or manufacturer too. Picking a technically good inspection body reduces the possibility of the further inspection being mandatory.
#4 Enhance your Customer Confidence
Self-assurance in a product is improved in case clients know it has been carefully assessed by an independent, capable inspection body.
This happens so in case an item supplier can show to their customers that the inspection body itself has been assessed by a third party.
Gradually customers are depending on independent inspection evidence, rather than just accepting a supplier’s word that the merchandise is “fit for purpose”.
#5 Lessen Charges and Enhance Acceptance of Items Worldwide
Through the Inspection authorization, officially competent, ascribed inspection bodies obtain global recognition, which lets their inspection reports to be more eagerly accepted in other financial prudence.
This recognition aids to lessen costs for builders and exporters by falling or removing the requirement for extra inspection in the importing economy.
#6 A Third-Party Inspector’s Role as Quality Consultant
It’s significant not to misinterpret the role of the inspector or inspection company in enhancing product quality at a factory.
The product inspector’s role is usually restricted to classifying quality flaws and non-conforming components. While an inspector may have years of experience confirming a certain product type, like headphones, that’s not to say they’re capable to point out the course that’s producing a defect.
At times a third-party inspector or inspection company can suggest procedures that might be paying to quality problems.
But for more multifaceted problems, it’s mostly better to employ a manufacturing consultant or other company competent to conduct a process audit. This course varies from a product inspection in that it emphases on the production procedures at a factory.
#7 Improved Relationships with Customers
When bearing in mind the advantages of third-party inspection for suppliers, enhancing the relationship you have with your contractor should be near the top of the list.
A carrier that doesn’t have any outside inaccuracy into the status and complaint of their order can’t be sure what they’ve paid for until they really obtain the finished goods.
Likewise, the supplier isn’t capable to get a response from their customer on the properties until the customer sees them. And an alteration between what the contractor and the importer believe is adequate is one of the main motives why the relationship between the two parties can turn bitter. Just get back to the example of headphones.
Maybe the factory staff catches the wiring matter by challenging a sample of the finished item that comes off the line. But maybe they don’t recognize that the press marks on the ear pads are an issue you can’t accept. The supplier might fix the elements affected by the wiring problem but disregard to address or notify you of those with press marks.
Now your level of limpidity is inadequate. You may have a well-developed QC inspection worksheet, but it doesn’t contain potential issues you weren’t well-aware of beforehand.
The supplier ends up delivering you the finished headphones without knowing there’s an issue with them. And your link with your supplier suffers because of a variance in product expectations.
Are you looking for a product inspection service?