What is a Deep Hole Called? Deep Hole Drilling and Gun Drilling Explained
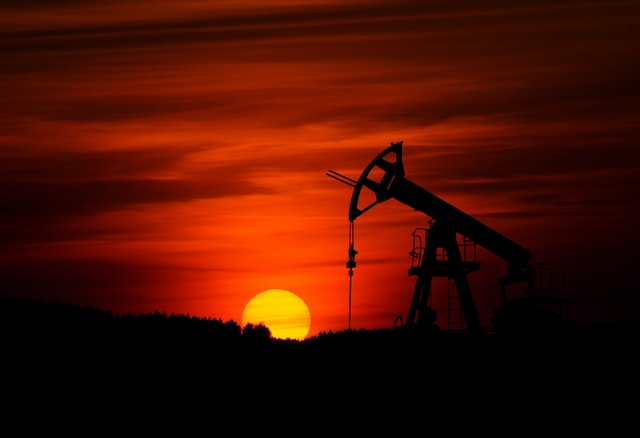
In the world of metal instruments, tools, and part fabrication, deep hole drilling involves the careful, accurate cavity creation within metal for industrial or mechanical purposes.
A gun or rifle barrel is probably the most commonly recognized form of deep hole drilling, but the cavity-creation application is regularly used for many other purposes such as tooling, components, detailed instrument parts, and similar.
Generally, a cavity is classified as a deep hole when it has a ratio of 10:1 with regards to depth versus diameter.
The need for a high level of accuracy, clean cavity creation, and very straight production makes the process an automated one in today’s settings, and the modern form of deep hole drilling is practically impossible to match by hand or manual application (although that’s exactly how it was created in earlier times and at a much slower pace of production).
Drilling With Very Specialized Equipment
No surprise, very specialized drilling tools are used to effect deep hole drilling on metal material.
Usually designed with an injected cooling system included, the drill component can work at very small but high-speed rotations, while the included cooling keeps the drill’s friction heat at a minimum inside the growing cavity being created.
The injected coolant also helps wash out the drill residue created from the contact point of the drilling process, removing the chance of unwanted damage inside.
Deep hole drilling processing can be applied in two different ways. The first is conventional; the removal of material and creation of the cavity is applied by a drill bit working its way through the target material from the outside in.
Alternatively, the material itself could be spun against the drill bit that stays stationary. This alternative option tends to be used where a drill point is bigger and can be used evenly through the tube or material, but the material itself needs to be secured better to avoid the problem of vibration and wobbling.
On a technical level, deep hole drilling is applied in two different procedures. One is known as BTA drilling and the other is gun drilling.
Gun Drilling Explained
What is a deep hole called in terms of equipment fabrication, such as specialized tubing? The gun drilling approach sounds exactly the way one would imagine, incorporating a long tool that goes inside a tube and routes out the internals to create the inner channel.
The diameter of such cavity creations can range anywhere from 1 to 50 mm inside in most cases, and the tool itself can drill and remove residue as it works deeper and deeper into the targeted material.
A normal drill would not suffice; the drill bit would typically be too short, and the rotational factor would cause wobbling, which in turn creates deviations in the tube and its expected straightness.
As mentioned earlier, the most commonly known form of gun drilling came from manufacturing firearms, particularly long barrel guns and rifles.
Originally done by hand, which also had something to do with the poor quality of many firearms, gun drilling has been taken over by machinery that has improved through the centuries to the fine, exact process it is today.
Borrowing from the lessons learned with early firearm manufacturing, alternative gun drilling has become a high-tech function that’s been applied to all types of tooling, from delicate medical equipment to fuel lines and injection mold spigots.
The process has even been attempted through CNC machining, with some limited success. 10:1 ratio of drilling is no longer the norm, with a 20:1 ratio quite possible. And, in some very extreme applications, tubes as small as 400:1 have been created accurately.
What to Expect from the Process and Related Technology
The application of gun drilling and deep hole drilling are best applied where equipment or parts are needed that must have accurate cavity clearing done for extended lengths and for specific diameters.
This process is ideal for parts that need to transit a set amount of fluid or gasses through a delivery channel at a set volume and rate without noticeable deviance.
Again, the most common sizing tends to be in the range of 3mm to 50mm, but smaller sizes are doable with specialized drill bits and equipment. Larger than 50mm cavities generally need to start moving into the realm of alternative drilling approaches instead.
Hiring the Right Help for the Job
Given the mechanical sensitivity of what’s involved with deep hole drilling and gun drilling, contracting out the necessary machining work isn’t going to be the kind of task trusted to just any provider.
Ideally, deep hole drilling tasks need to be acquired from providers with a significant depth of experience in the work as well as the appropriate specialized equipment on hand to do the job right the first time with a high degree of accuracy and quality.
That kind of service is provided by Acrodrill, a leader in deep hole drilling with a reputation that has been earned over time with professional work and repeat accolades on the finished product provided by satisfied customers.
Acrodrill prides itself on maintaining the best practical deep hole drilling tooling possible as well as maintaining a high standard of training among its specialists for just this kind of work.
When looking for deep hole drilling near me, consider the fact that Acrodrill products are some of the most competitive pieces made via deep hole drilling, ranging from highly delicate pieces to transit conduits with highly accurate straightness for the least amount of traffic friction possible.