4 Ways To Nail Your Machining Processes
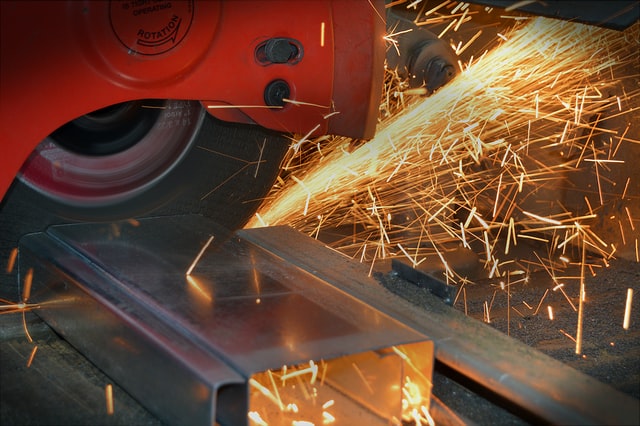
Machining something to perfection is impossible because of the material qualities of metal. But with the right equipment and approaches, you can get pretty close.
Being able to machine accurately increases your value to the people you serve and also allows you to charge a premium.
Having great machining ability in-house can save you from having to seek out specialist suppliers and reduce delays.
But how do you machine items like a professional? Let’s take a look.
1. Use Lasers
Equipment is only as accurate as of its ability to measure. So if you’re measuring parts with a meter rule, you’re never going to get close to industry accuracy standards.
The best approach to accuracy is to use a laser. Lasers let you know precise distances and are perfect for measuring the quality of machines, their calibration, and whether you need to service them or not.
Lasers are great for letting you know whether the machine’s accuracy can be improved. For instance, suppose you tinker around with the machine for a couple of days as part of its annual service.
During that time, you attempt to calibrate it to give you a certain level of cutting accuracy. With a laser measuring device, you can figure out whether you are bumping up against the limits of the machine or not.
2. Improve Maintenance Schedules
Human involvement can degrade the accuracy of your machining processes over time. The more workers interact with a tool, the more likely its accuracy will suffer and it will start to degrade.
Fortunately, keeping a regular maintenance schedule can help. Simply getting engineers to return the machine to its desired factory calibration helps to keep it functioning as it should.
3. Improve Automation
You can also improve accuracy by replacing human operators with CAM. Getting machines to move machines typically results in less wear and tear, and more accuracy.
Many broach machine manufacturers build their devices so that they contain all of their moving parts in a controlled environment. The operator simply pushes buttons on the exterior of the machine. Servos and other mechanical devices control the cutting action, negating the need for direct human muscle involvement.
If you find that you are still struggling with accuracy, it can be helpful to place reference points in the future. Tooling bars and features make it easy to establish X-Y-Z points for fixtures and fittings.
You can then visually inspect items to ensure that they are moderately calibrated without having to open up machines and go fiddling around inside.
4. Monitor Your Ballbar
While lasers are great for in-depth calibrations, bullbars are perfect for collecting a variety of performance data on the fly.
By inspecting your bullbars, you can check for changes and confirm that the machine is still operating at its intended baseline level. Ballbar inspections take place outside the cut.
Additional CNC capabilities include things like adaptive control and tool management. It is also good for in-process inspection.
You are able to use it to inspect the part when the work is done or incorporate it into the tool’s self-diagnostic equipment.